Even if Ralf Deiterding had gazed into a crystal ball when deciding what to study in his native Germany, he couldn’t have made a better choice for the work he does today.
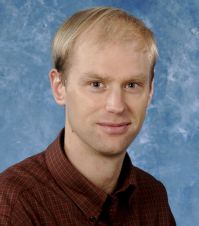
Ralf Deiterding, Oak Ridge National Lab
“My diploma is in applied and technical mathematics,” says Deiterding. “It’s 60% math, 20% computer science and 20% mechanical engineering. I focused on solid mechanics and fluid dynamics.”
It’s ideal for his current job: simulating detonation and shock waves in various scenarios at Oak Ridge National Laboratory (ORNL). Deiterding holds the Alston S. Householder Postdoctoral Fellowship in Scientific Computing, which is supported by DOE’s Office of Advanced Scientific Computing Research.
Deiterding’s work combines a number of disciplines: developing and applying innovative numerical methods, scientific computing on high-performance DOE supercomputers, visualizing results, and interpreting physical phenomena.
In one ASCR-supported project, Dieterding and his fellow researchers are creating a high-resolution simulation of a detonation wave in a hydrogen-oxygen gas mixture to better understand the underlying mechanisms of possible explosions in refinery pipelines.

The simulation shows the front of a detonation wave traveling through a 60-degree pipe bend. The computational grid is refined on the fly to capture the evolution of the triple points. The color plot shows a snapshot of the temperature field; the gray scales above indicate areas of increasing mesh resolution.
A detonation is a combustion wave caused by a shock. Compression from the shock raises the temperature above the ignition point for the chemical reaction that drives combustion – it is that reaction that drives the shock itself forward. The energy balance between the shock and the chemical reaction is unstable, so detonation waves don’t remain in a single plane.
“Unstable shock waves spread perpendicular to the detonation front,” Deiterding explains. “You get triple points – places where the detonation front and transverse shocks intersect. At these points, pressure can increase by a factor of five and temperature rises as well.”
Experimental work shows that the triple points often move in “fish-scale” patterns. The rotational flow of the fluid increases locally, which researchers can use to track the triple points. The key to accurately simulating detonations – and, in the end, to making pipe installations safer – is correctly tracing the evolution of these areas. In fact, one reason Deiterding is confident in his simulation results is that the same number of triple points reappear after the bend.
To develop these simulations, Deiterding collaborated with several experts in detonation and compressible gas dynamics, including Drs. Joseph E. Shepherd, Dale I. Pullin and Hans G. Hornung, all from the Graduate Aeronautical Laboratories at the California Institute of Technology (Caltech).
But the techniques Deiterding developed have uses far beyond pipes. “Software that simulates detonation waves also has application to other kinds of problems related to shock waves,” he notes.
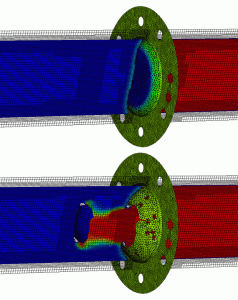
In this fluid-structure interaction simulation, a pressure wave generated in a water shocktube ruptures a thin copper plate. The simulation mimics the effect of an underwater explosion.
One such problem involves thin copper plates rupturing when a pressure wave hits them. Deiterding developed the Virtual Test Facility software for this simulation when he worked as chief software architect for the DOE Advanced Simulation and Computing Center at Caltech. The simulation mimics the effect of an underwater explosion on a small part of a ship’s hull, a problem of keen interest to the Department of Defense. Deiterding’s collaborators included Dr. Fehmi Cirak of Cambridge University and Dr. Daniel Meiron of Caltech.
The same fluid-structure interaction software also will help solve a critical problem at ORNL. The lab is home to the Spallation Neutron Source, a particle accelerator that produces the world’s most intense pulses of neutrons, that is supported by the Office of Basic Energy Sciences within the DOE’s Office of Science. Recording how neutrons scatter when they hit a sample gives scientists insights into materials at the molecular level.
But to generate neutrons, high-energy pulses of protons must strike a heavy-metal target enclosed by a container filled with liquid mercury. Shock wave interaction creates fluid cavities that severely damage the container walls. That, in turn, limits the beam power available to researchers. Deiterding is working with Dr. Bernie Riemer and Dr. Mark Wendel of ORNL to develop a simulation that will predict the shock-induced structural loadings.
Although the chemical and nuclear industries and the military could provide an endless supply of problems for Deiterding to solve, the ones he chooses share one essential characteristic.
“With software development going on for 20 to 30 years, it’s sometimes hard to find scientifically rewarding applications,” he says. “So I look for areas where the simulation software is underdeveloped. That gives me a good reason to propose projects. The main problem is usually mathematical, but I have the further luxury of writing new software.”